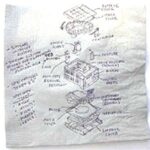
The Best Time for Noise Control Design
#4 – We’ll add the noise control afterward, if needed
Noise control added after the fact has a nasty tendency to make equipment
- bulky,
- heavy,
- expensive,
- inefficient, and
- difficult to assemble and maintain,
- with extra parts to keep track of.
It also can make it run some combination of hot, slow, and/or weak.
Noise is a waste byproduct – to corral that noise in a compact way, it’s necessary to get close to where the noise is generated or to block its escape. In an air-breathing machine, the airflow can be throttled – power must then be increased to make up for the loss. Result? Little noise reduction, more power consumed. In enclosed machines noticeable noise reduction can require dramatically increasing the surface weight; then you get to manage the confined heat.
Noise emission depends on the total power and the efficiency of conversion to sound. The best way to reduce noise is to reduce one, the other, or both. The best time to optimize the process so that it’s “quiet by design” or “intrinsically quiet” is in very early design stages – about the time a rectangle is drawn on a napkin at lunch. Design inertia increases exponentially after that. Why wait until it’s too late?
Here’s an article about a product that wasn’t too late to save: Engineering a quieter leafblower
The necessary skills can however be learned by mere mortals. Nelson Acoustics provide practical training in noise control.
Nelson Acoustics can help you anticipate and manage the quantity and characteristics of emitted sound to minimize annoyance. Before it makes the news.
Copyright 2024 Nelson Acoustics